I went outside today and was amazed at the difference a few days makes.
 |
This didn't look like this 3 days ago. |
Just a couple days ago, I was waxing philosophical, wondering what grilled groundhog tastes like, for that little bastard got the timing of spring all shades of wrong. Alas, we hit 72 degrees today; the snow's gone, so are the winter doldrums. The faint smell of summer was in the air: budding trees, lillies, and lilacs. What could possibly be missing from such a sweet and serene scene? Why, bubbling lead, plastic, and adhesive, of course!
 |
Who needs lilacs when you can have lead? |
Enthused, I broke out the safety gear and the components of my smelter and hooked it all up together. The smelting equipment was pretty bare bones but worked
well. I got
the idea for the setup from the good old boys of West Virginia, the same
fellas who melt tire weights for buckshot and fishing lures. They know
what they're doing; some claim they've melted tons of lead. How? Slowly,
carefully, and courtesy of Wal Mart. My burner is a double camp stove
from Coleman, one that uses standard 16.4 oz propane tanks. I was in the
market for one anyway, so the $30 was worth it.
 |
The foundry, courtesy of Wal Mart. Keel nose block awaits the pour. |
The cast iron
skillets came as a set of 3. I used 2 in this effort, saving the
largest one for something that might resemble real cooking some day. The
key to these skillets is the little lip for the pour. You definitely
want to be able to guide the pour evenly. I was not disappointed. The
handle was a little short, making grasping this a little on the delicate
side. But the skillets held up under the heat and was just big enough
to manage the weight of the lead. Finally, an important component is the
scraper. I used a stainless steel egg turner. I have seen some fairly complex smelting set ups and I can say with certainty that it's not needed.
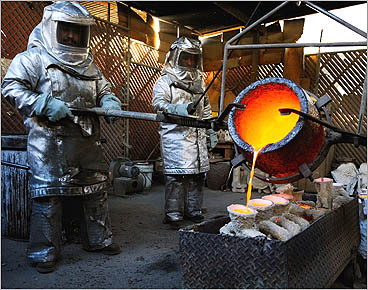 |
Yeah, this might be overkill. |
I knew it'd be a day-long project (judging from other bloggers) so I set about early. I quickly settled into a rhythm: do a couple melts and pours, work some emails, do some more melts and pours, some lunch, an in depth discussion on a major work deliverable, melts and pours, and finally, relief. Part
of the relief is that lead is heavy. It's quite a work out. It also took a few sessions to get into the rhythm and to understand how much to do at any one time. Smelt too much and you may not be
able to control the pour. Smelt too little and you might be spending the
better part of a week getting the requisite number of pounds.
I started with the centerboard with the eBay lead. I was surprised how well it melted. I set a timer for 6 minutes and it was melted in 4. By the way, melted lead is really pretty. Silky smooth, it looks like liquid mercury but more silvery. I'm on the lookout for one of those cast iron corn cob things so I can make lead weights from the leftover, as setting up the smelting stuff is a pain and while it's there might as well melt some more stuff.
 |
Centerboard with one pour to go. Will add epoxy and sand smooth. |
With the centerboard done, I set up the keel. That was a bit of a balancing act. I melted and poured the remaining of the nice eBay lead then started on the tire weights. Not sure what to expect, I got everything I thought and more. Wow, that stuff is nasty. If I could spell carcinogen I would. I'm not surprised people give up at this point and run out and buy $260 worth of pure lead shot but I think that's a bit of an overreaction. As long as this is done outside, away from delicate things like people and pets, and you're wearing a respirator and full safety gear, it's not so bad. It took around 10 pours to get the 90+ pounds of the keel aft section done. I did all of this at one time, but there's no reason for that, as the manual says. A technique I picked up towards the end was to skim the major dross off the top of the melt, then carefully add another handful of weights. With lead already melted, the new stuff melts pretty quickly and you've got an instant 2-3 pounds with very little extra work.
 |
Lead will smoke and bubble when first poured. Smells like camping. The bubbles are to ensure the pour didn't disrupt the levels. |
 |
Finished keel nose block. This will be leveled with epoxy before the keelson gets attached. |
 |
The aft part of the keel about half-way poured. Took a break here for lunch. Notice the bow in the middle. |
 |
Omelette please. Bacon, sausage, and extra tire weight clips. The long weight in the middle was not lead after all. |
 |
First bucket (plus eBay stuff) done. |
A few things to keep in mind if you're going to try this. Just to reiterate: you absolutely, 110%, must have a good, working respirator. The stuff that
bubbles off spells cancer as it
floats above the lead. You must also have good welder's gloves, eye
wear, face shield, long pants, and long sleeves. There's no point in
risking life and limb for this. Suit up and be diligent.
Another thing you may have noticed in one of the photos above is how the long length of the keelson looks a little squeezed from the clamps and landscape bricks. I didn't notice this when I was first poured, but only much later when I was about to secure the cap. It turned out I had a good 1/4" at least on both sides when the wood came back out, meaning I poured too little lead. A later post details this adventure.
An easy fix here, if these are the materials you have, would be to clamp a 2x4 or something similar the length of each side, then clamp on the landscape bricks. This will even out the pressure of the squeeze and won't collapse in the middle as I did here. Lesson learned!
 |
I'm not wearing pants. |
The lead pour is one of those things every PocketShip builder reads about and isn't sure it can be pulled off. Experiences range from "
worst ever" to "
wasn't so bad" to "
I smelt for fun". I'm towards the latter end of that. To say I enjoyed it would be a stretch. I think what I enjoyed more was the idea that I sourced these tire weights, sorted them, melted them, skimmed them, and they are now a permanent part of the boat. This means I can finally finish up the centerboard once and for all, and get the keel ready for the crate. I'm just about done with this phase of the build and it feels awesome!
No comments:
Post a Comment